Co-processing of Cement Kilns
What is Co-processing of Cement Kilns?
Under global climate change and environmental pressure, traditional waste treatment faces challenges. Cement kiln co-processing technology utilizes the high temperature, high turbulence, and long retention time characteristics of cement kilns to transform waste into alternative raw materials and fuels for cement, achieving a zero-waste environmental goal. According to research by the World Business Council for Sustainable Development (WBCSD), the high temperatures of over 1,300℃ in cement kilns can completely decompose and resource waste, and also break down dioxins that incinerators cannot handle, making it an efficient and environmentally friendly waste treatment method.
.png)
Processing Flow
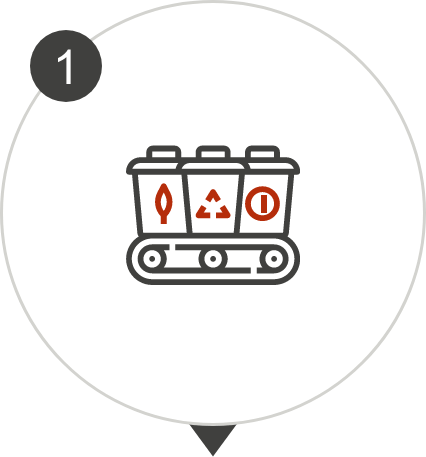
Waste Pretreatment
After household waste is sorted and compressed, it is sent to the TCC gasifier for further processing.
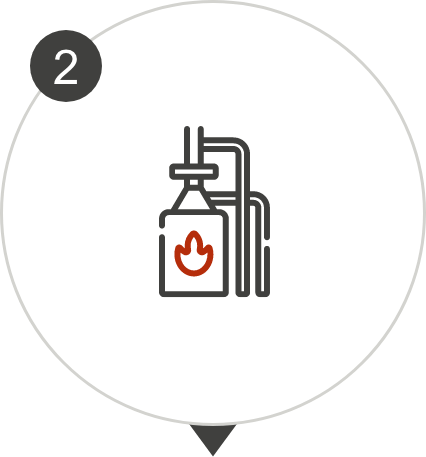
High-Temperature Gasification
The gasifier decomposes waste into combustible gas and bottom ash.
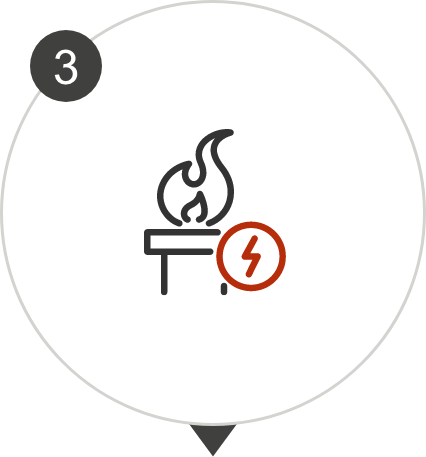
Energy Recovery
Combustible gas is fed into the cement kiln for combustion as an alternative fuel.
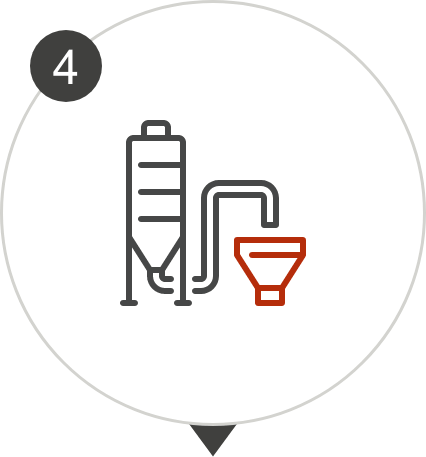
Harmless Treatment
Bottom ash is mixed with cement raw materials and undergoes high-temperature calcination to become cement kilns.
Resource Recycling and Environmental Benefits
1
Coal Reduction
The heat value generated from the waste treatment process can replace some coal-based fuels, effectively reducing carbon emissions.
2
Waste Reduction
A maximum of 200 tons of domestic waste can be processed daily, reducing the need for landfills.
3
Carbon Reduction
Avoiding the accumulation of waste prevents methane emissions, thereby reducing the impact of greenhouse gases.
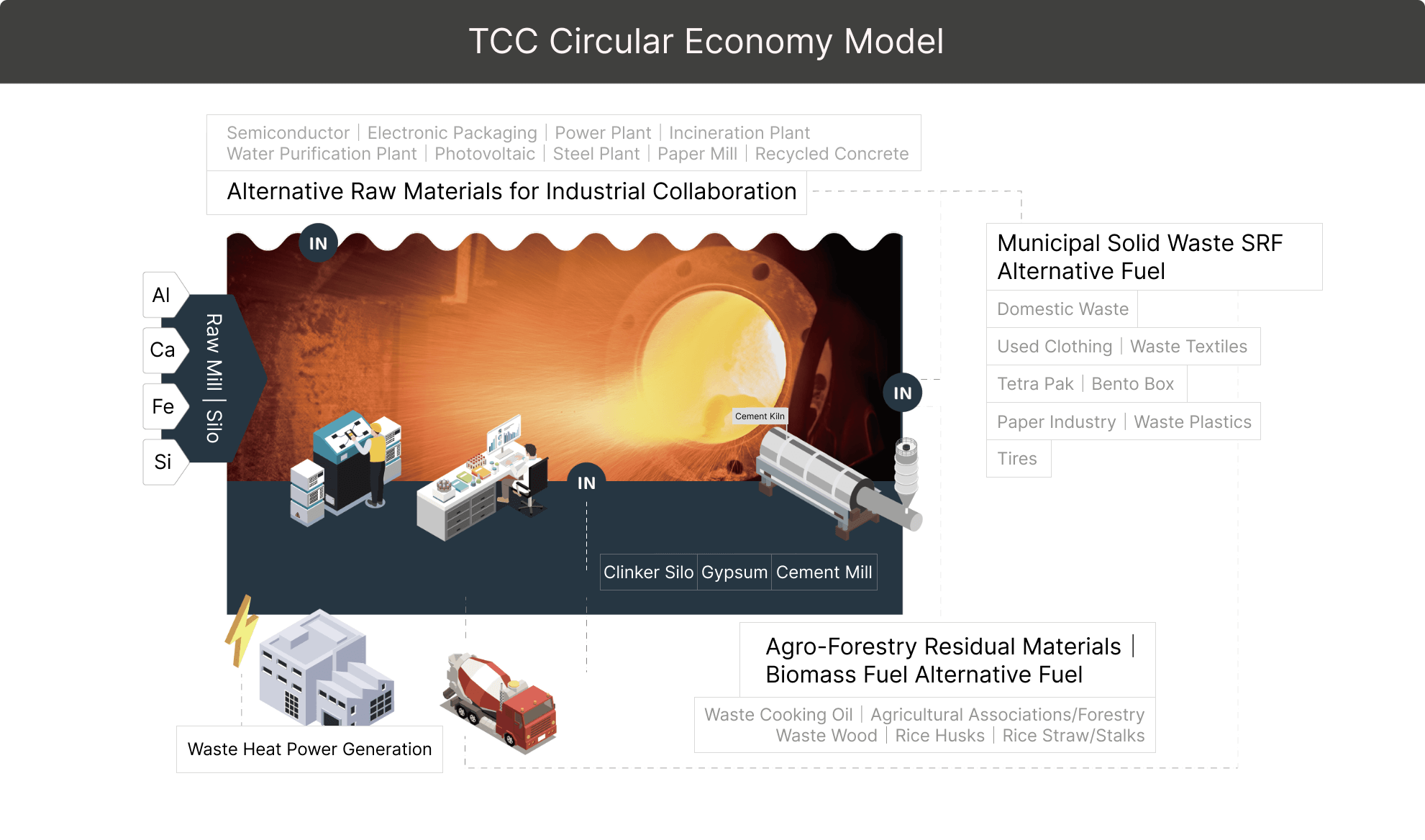
Waste Harmlessness and Resource Recovery
TCC leverages the advantages of high-temperature co-processing in cement kilns to render waste harmless and repurpose it. This diversifies cement plant revenue streams and deepens partnerships with local governments and industry collaborators. These wastes then become alternative fuels and raw materials for the cement production process, transforming into renewable resources. This strengthens TCC's competitiveness in resource circulation, helping them reduce carbon emissions in their processes, truly achieving both waste and carbon reduction.
.png)
Technology | Co-processing of Cement Kilns | Traditional Waste Incinerator |
---|---|---|
Processing Temperature | 1,300-1,800°C | Between 850 and 1,050°C (According to data from the Ministry of Environment) |
Residue Generation | No bottom ash and fly ash | Fly ash and bottom ash are required to process. |
Waste Management | Transformation into alternative raw materials and fuels for the cement manufacturing process | Processing general household waste |
Environmental Performance | Complies with circular economy and reduces carbon emissions. | After combustion, additional treatment of pollutant is still necessary. |
TCC's Co-processing of Cement Kilns
TCC's plants on both sides of the Taiwan Strait already have the technology to co-process waste or domestic waste using the high temperatures of cement kilns:
Plants in Mainland China have assisted in processing 5,631,708 tonnes of industrial waste.
5,631,708tonnes
Plants in Taiwan have assisted in processing 974,197 tonnes of industrial waste.
974,197tonnes
Achieved the highest level of BS 8001 Circular Economy Optimizing.
TCC's Path Towards Carbon Neutrality and Carbon Reduction Verification
Important Milestones
2018/12
2020/12
2022/12
2024/12
Successfully passed BS8001:2017 Organizational Implementation of Circular Economy Framework Guidelines with the theme of Business Waste Reuse and Treatment.
Achieved LEVEL 4 verification: Optimizing, became the first cement company to receive this certification.
Successfully passed the re-verification of BS 8001:2017 Organizational Implementation of Circular Economy Framework Guidelines with a focus on of Expanded Use of Alternative Raw Materials/Fuels in Cement Manufacturing Process.
LEVEL 4 Verification: Optimizing
Successfully passed BS 8001:2017 Organizational Implementation of Circular Economy Framework Guidelines with a focus on Carbon Reduction Verification of Alternative Raw Materials and Fuels on the Path to Carbon Neutrality.
Third LEVEL 4 Verification: Optimizing
MSW Resource-to-alternative fuels and raw materials circular model